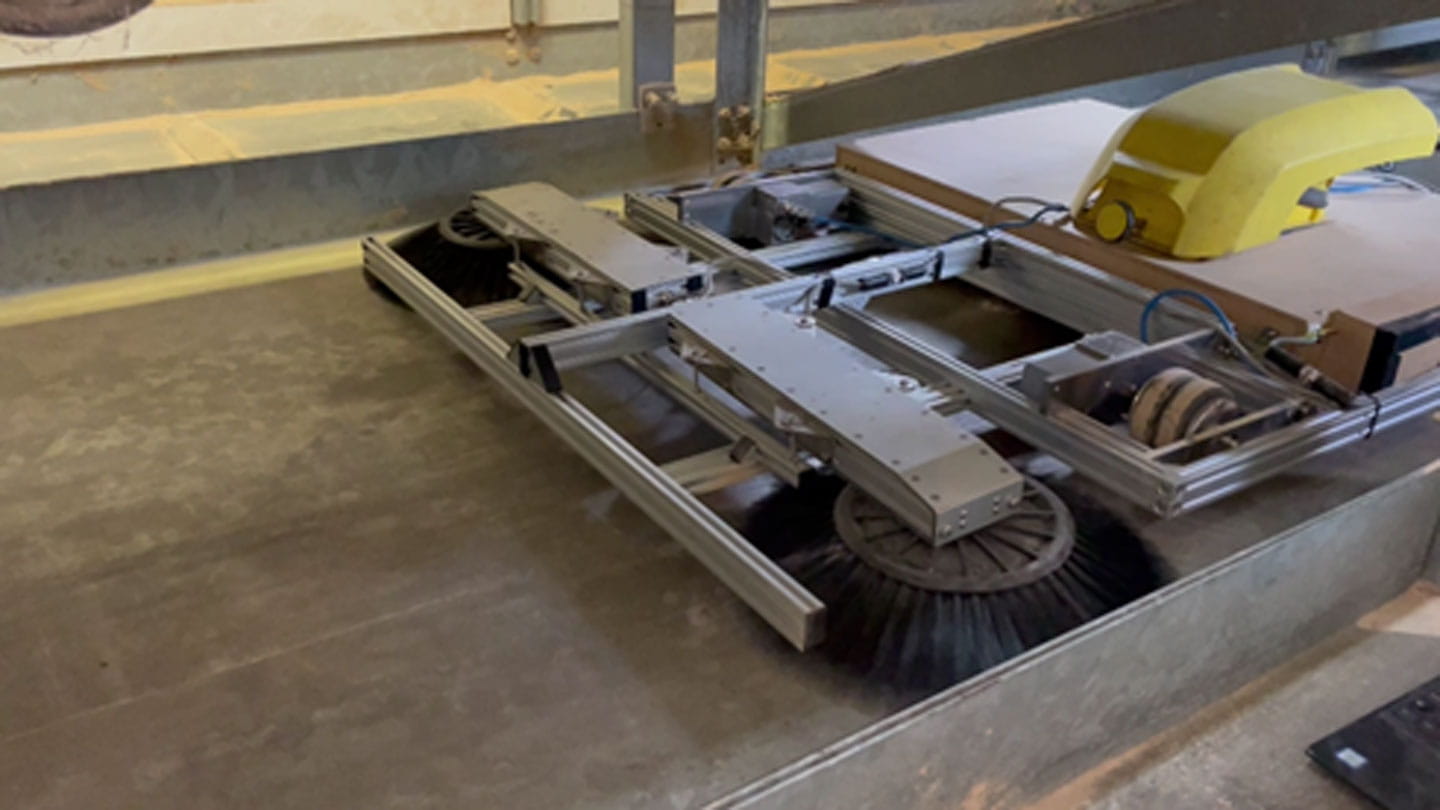
New robotically cleaning machine
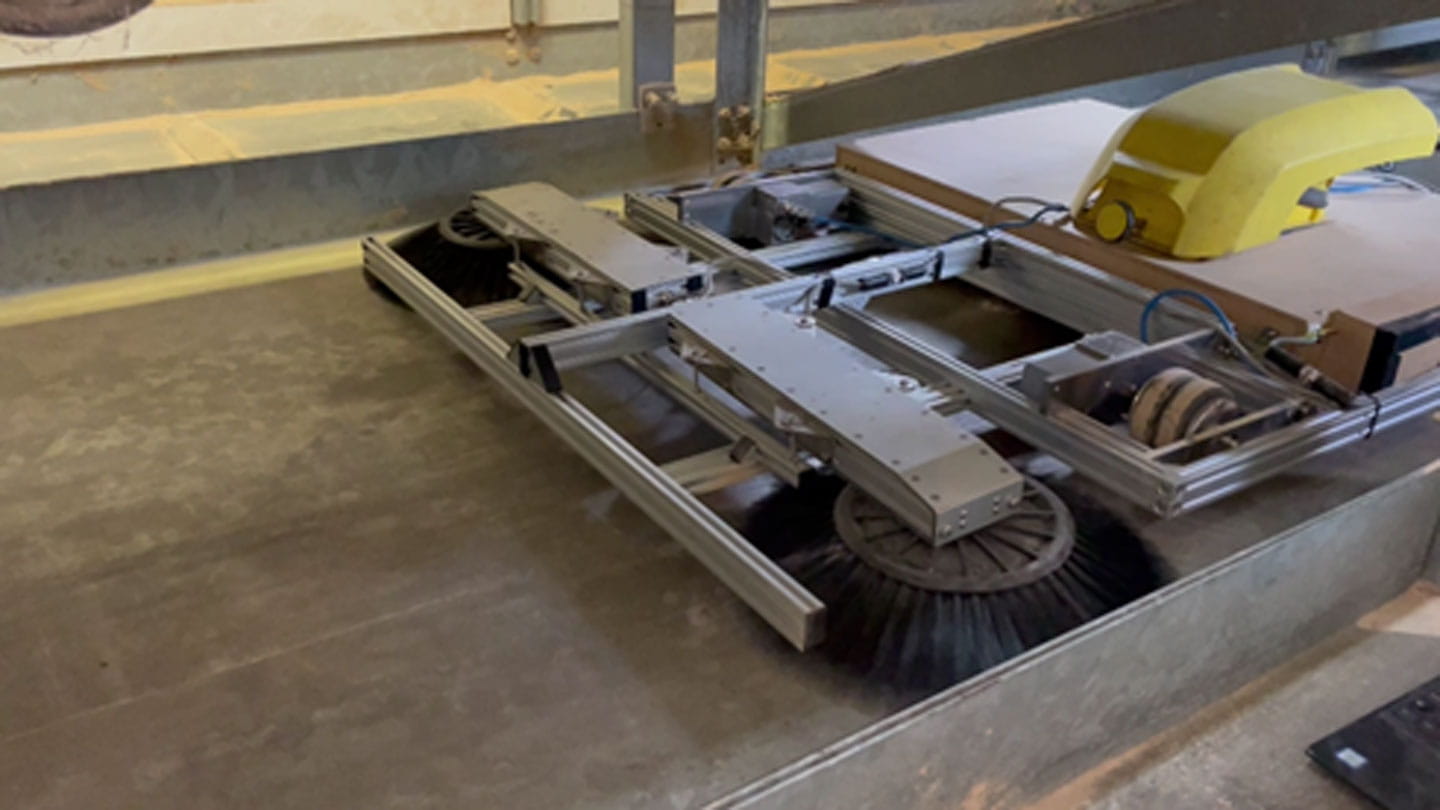
The background is that frequent removal of dust coming from the biomasses in the areas under and along the wood pellet transport lines and in biomass handling areas lower the risk of explosion and fire spreading by reducing the amounts of deposited dust. For safety reasons, manual cleaning of these areas and conveyor belts is not allowed during operation of the transport system.
In addition, one daily manual cleaning of dust allows ~24 hours for new dust to settle on surfaces. Finally, commercially available robot dust cleaners are not suitable for cleaning under conveyor belts.
Hence the aim has been to develop a flexible, fit for purpose robot cleaning solution.
Ørsted Bioenergy and Thermal Power A/S has developed a robot cleaning machine for cleaning of dust and smaller particles (e.g., wood dust, straw dust, and wood pellets) at power plants. The Danish Technological Institute has headed the development of the robot as a consultant to Ørsted.
The robot is designed for cleaning of all surfaces but is particularly well suited for cleaning under conveyor belts, transporting wood pellets from the wood pellet storages to the combustion boilers.
The robot has an optimized flat design, making it possible to clean under low-height structures.
The cleaning concept is based on sweeping and vacuuming. The robot is equipped with rotating brushes, placed at the front edges of the robot. These brushes guide the material to a centrally placed roller brush that transports the material to the dust compartment. The cleaning is furthermore aided by a vacuuming system to remove the finer particles.
The robot operates as an Automated Guided Vehicle (AGV), using ultrasonic distance sensors to maintain a straight course. Hence no wire pull or guide rail in the floor is necessary.
The main features are summarized below: